- Ku Wiśle 7, 00-707 Warsaw
- +48 787 783 590
- biuro@interprocess.pl
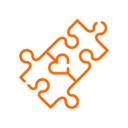
Comprehensive Project Implementation
We supervise the entirety of each implemented project. We provide full support at every stage of the investment, and after the launch – also service.
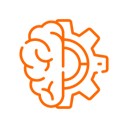
Innovative Solutions
Our focus is on intelligent process automation and the high added value of each investment, both in terms of quality, improved safety and productivity.
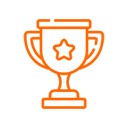
Many Years of Experience
We draw on nearly 20 years of experience in the design, manufacture and implementation of bulk material handling equipment in various industries.
Our solutions
Volumetric and
gravimetric dosing
Our company will provide modern solutions in weight automation for existing installations as well as high-quality screw and vibrating feeders. The mass loss in the tank defines the material flow. In connection with the PID control loop, we will receive a feeder with exceptional accuracy.
Big Bag filling
and emptying
The use of special transport bags in the industry called BIG-BAGs is now very practical. Our constructions ensure an efficient process of filling and emptying bags with minimal involvement of employees. The elements massaging the material and tight connection make the whole process easy, fast and dust-free.
Transport
of bulk materials
We provide our customers with solutions that make moving dry bulk materials such as powders and granules more efficient and effective. Vacuum transport is easy to keep clean, minimizing operation and maintaining a fluid-free working environment even in potentially explosive areas.
Filling
and packaging
Our measuring systems are characterized by high speed and high measurement resolution. All this in order to maintain exceptional accuracy and prevent overfilling. This applies to processes at both the micro level and filling large bags. For larger parts, every gram matters, and our customers save money.
INTERPROCESS OFFER
Our offer of technological solutions for weighing, dosing, mixing and transporting of bulk materials, many years of experience and comprehensive technical knowledge make us the ideal partner for cooperation. We support our customers throughout the entire process until the installation is started and the employees are trained. We provide comprehensive after-sales service as well as spare parts. We provide devices and complete installations for complex production processes