- Ku Wiśle 7, 00-707 Warsaw
- +48 787 783 590
- biuro@interprocess.pl
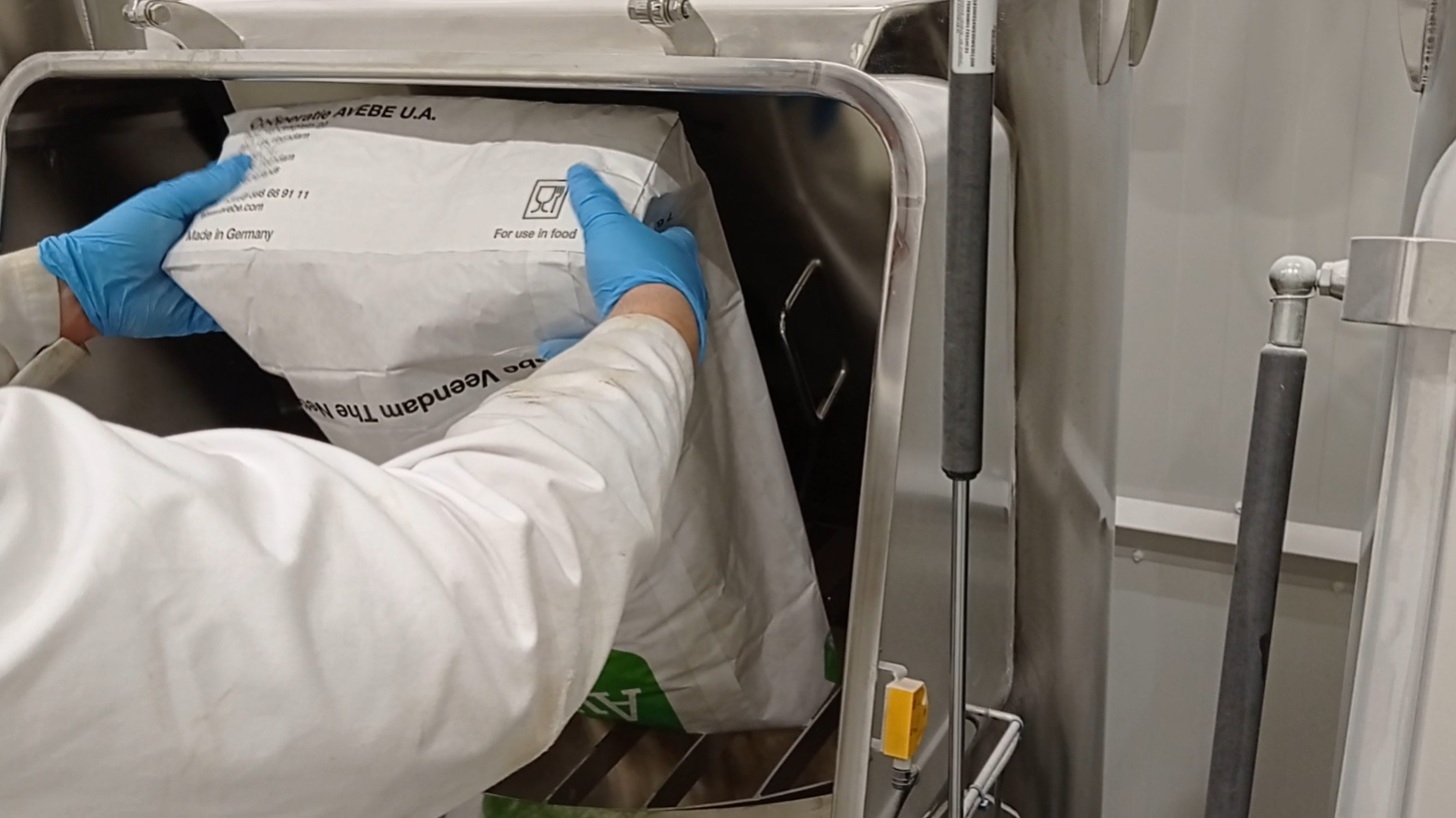
Our task is to make all types of processes related to the processing of bulk materials simple and trouble-free. During the seemingly simple task of emptying small bags, the problem of dust formation is a common phenomenon. The STB stations we produce are a convenient solution to this problem.
The device is intended for solids delivered in sacks with a capacity of up to 50 liters. They provide a convenient way to empty and feed small amounts of product into the main process – e.g. a mixer or transport system between two distant points in the process installation. They are a safe solution that helps avoid spine injuries and minimize dust generation.
Thanks to their modular design, they can be equipped with a number of additional devices such as: a compactor for empty sacks, a rare earth magnet, a rotary valve, a bottom suction unit or a screw feeder.
A built-in exhaust fan with a filter system with a reverse jet filter cleaning function help keep the equipment clean.
Offer
STB-V1 – sack tipping station
Specification:
- SEW exhaust fan 1.1 kW 3×400 / 3×500 VAC,
- cartridge filters with an area of 8-12 m2,
- automatic filter cleaning, using the built-in controller and 6 bar compressed air,
- a comfortable top for easy bag positioning and a charging grate (for safe unloading),
- a damper equipped with gas springs and a position sensor activating the exhaust fan or sequential filter cleaning.
Execution:
- 304 stainless steel (glass or electropolished),
- 316L stainless steel (glass or electropolished).
Applications:
- various types of dusty solids, e.g. fine-grained and coarse-grained powders, grains, granules

Download:
Options
- Station with a built-in fan
- Station without a built-in fan, using an external dust extraction system
- Empty bag compactor
- Rare earth magnet
- ATEX version for zones 21 and 22.
- Sack tipping support devices:
– fluidising pads
– vibrator
The lower part of the station can be used with:
- screw feeder
- rotary valve
- pneumatic transport
- butterfly valve or knife gate valve
- suction lance
STB-V2 – sack tipping station
Specification:
- exhaust fan 0.75 kW 3×400 VAC,
- cartridge filters with an area of 8-12 m2,
- automatic filter cleaning, using the built-in controller and 6 bar compressed air,
- a comfortable top for easy bag positioning and a charging grate (for safe unloading),
- a damper equipped with gas springs and a position sensor activating the exhaust fan or sequential filter cleaning.
Execution:
- 304 stainless steel (glass or electropolished),
- 316L stainless steel (glass or electropolished).
Applications:
- various types of dusty solids, e.g. fine-grained and coarse-grained powders, grains, granules
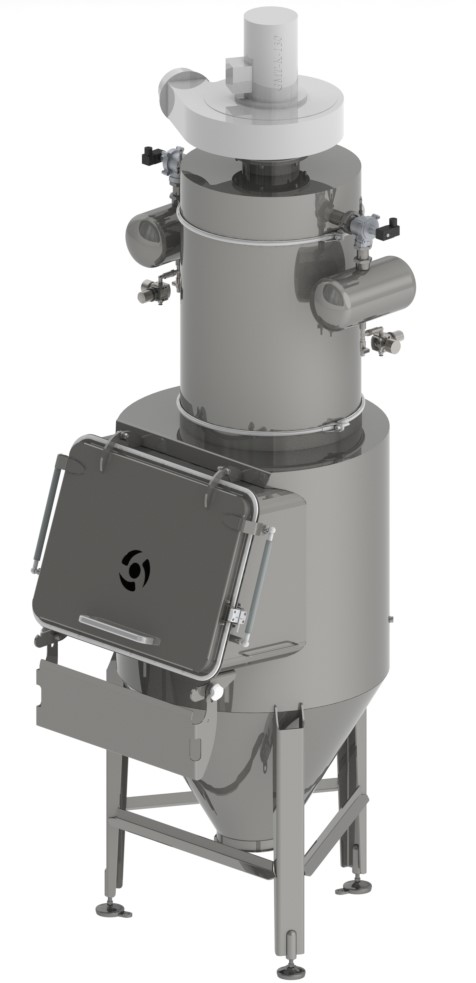
Download:
Options
- Station without a built-in fan, using an external dust extraction system
- Rare earth magnet
- Empty bag compactor
- ATEX version for zones 21 and 22.
- Sack tipping support devices:
– fluidising pads
– vibrator
The lower part of the station can be used with:
- screw feeder
- rotary valve
- butterfly valve or knife gate valve
- suction lance or bottom suction unit
- vibratory sieve
How does it work?
Step 1: the operator opens the hinged hatch that starts the exhaust fan.
Step 2: The operator places the bag on the station’s top inside the station, then cuts it open and pours the contents directly into the station’s tank (or the device below). The air flow generated by the exhaust fan causes the dust from the discharged material to be pulled into the center of the station.
Step 3: the dusty air is filtered through the cartridge filters inside the station. After unloading, the operator closes the hatch. The dust deposited on the surface of the filters is blown away by sequentially working compressed air nozzles. Automatic filter cleaning takes place only when the lid is closed and the fan is not running, so as not to create additional dust during unloading.
