- Ku Wiśle 7, 00-707 Warsaw
- +48 787 783 590
- biuro@interprocess.pl
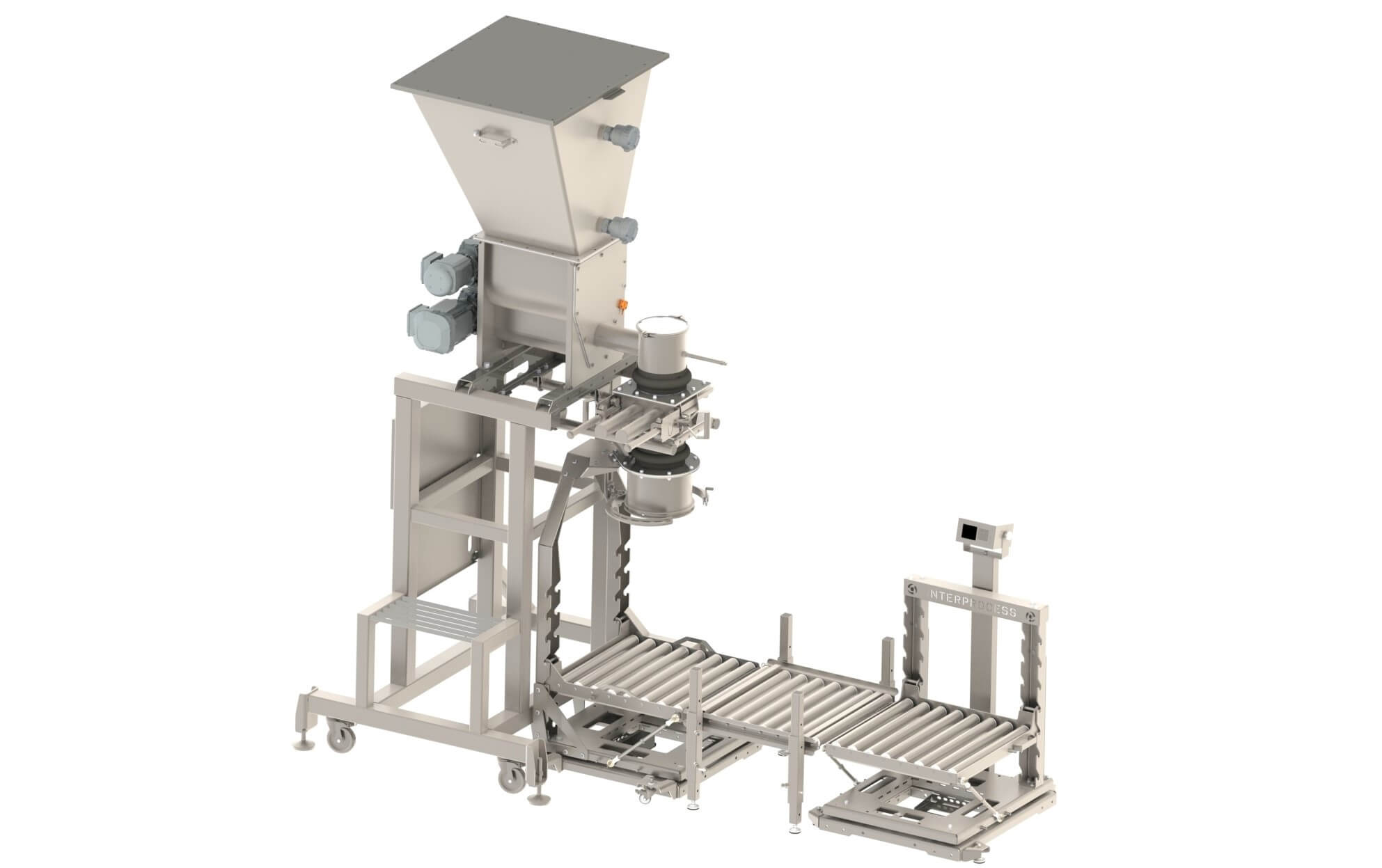
Filling & packaging lines
When producing bulk material mixtures and filling packages with relatively small portions, very high accuracy and filling speed are required. It is important to use a universal system that meets the requirements of customers in a practical way – it works great as a device for dust-free filling of various types of packaging, such as cardboard boxes or barrels of different weight – from 10 to 100 kg. At InterProcess, we approach each project individually, taking into account all the wishes and needs of the client, with attention to the smallest details. The carton and drum filling line meets strict hygiene requirements and guarantees easy handling. Depending on the customer’s needs, it is possible to design the device in accordance with the ATEX directive or FDA requirements.
The station for dust-free filling of packaging can be installed directly under mixers, buffer tanks or the material can be fed from a BIG-BAG. The main element of the entire line is a volumetric screw feeder, which provides control over the filling process with a hopper with geometry facilitating material flow, which is equipped with two fill sensors – a minimum and a maximum. After reaching the minimum value, the system automatically fills the hopper to the maximum value, without interrupting the filling process. Thanks to various types of sifters, we are sure that no foreign particles will be in our packaging. Depending on the type of container being filled (bags, boxes, barrels), the station can be equipped with various filling heads equipped with an inflatable seal, which ensures a tight connection and a dust-free filling process. An additional line is connected to the dust removal system. Thanks to the modular design, it is extremely easy to customize it. It is a universal solution for various dimensions of containers due to the system of quick change of distance between the rollers and the filling head. Our lines can be equipped with wheels, so they can be freely moved around the plant. On the presented model, we have equipped the device specially at the customer’s request with an additional, legal-for-trade scale.
How does it work?
In the case of bags or boxes with inserts, the filling process is handled manually. The operator puts a bag or foil from the box on the filling head, closes the clamp and with a foot switch turns on the process of pumping the seal, making the connection completely tight. Then it starts the dust-free filling process with a second foot switch. Dosing takes place automatically until a certain weight is reached, after which the system unseals the connection, thus allowing easy detachment of the container. The system can also be designed for fully automated operation when filling rigid containers, such as barrels, for example.
Refilling material without stopping the process
The product is fed to the main trough of the screw feeder from a hopper with a geometry that facilitates the flow of material equipped with two level sensors – minimum and maximum. After reaching the minimum value, the controller automatically starts filling the hopper to the maximum level without stopping the packaging process.
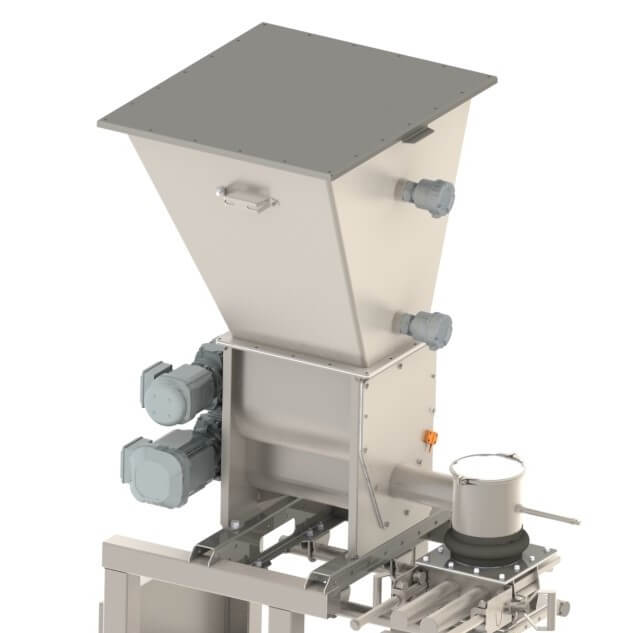
Material flow support
Screw feeders are equipped with a horizontal electric agitator driven by a separate electric motor, operating at a constant rotational speed, which ensures complete filling of the feeding tool and protects against material hanging. For products that are particularly difficult to fed, it is possible to install an additional vertical agitator.
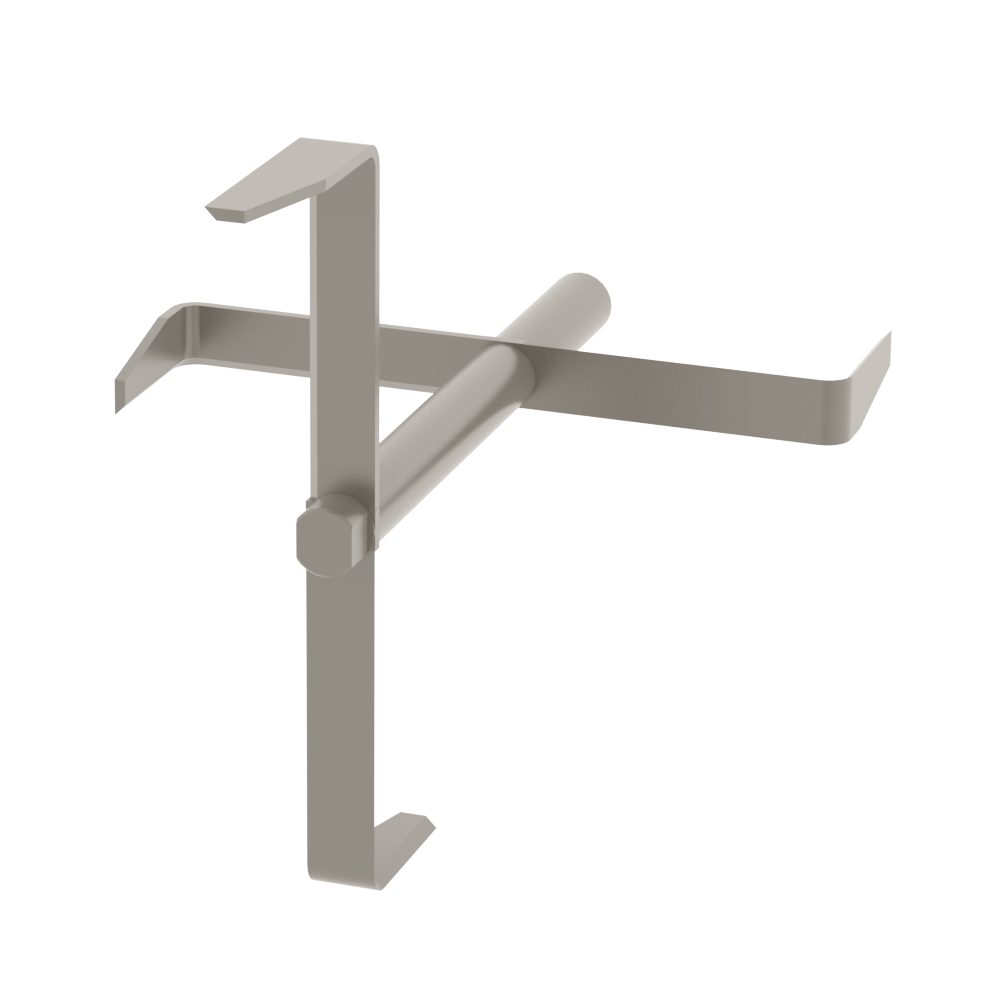
High accuracy scales
At InterProcess, we know how to use load cells in the most optimal way and our scales are reliable solutions for weight measurement. We offer platform scales of various sizes, also legal-for-trade, made of carbon steel and stainless steel tailored to the needs of our customers.
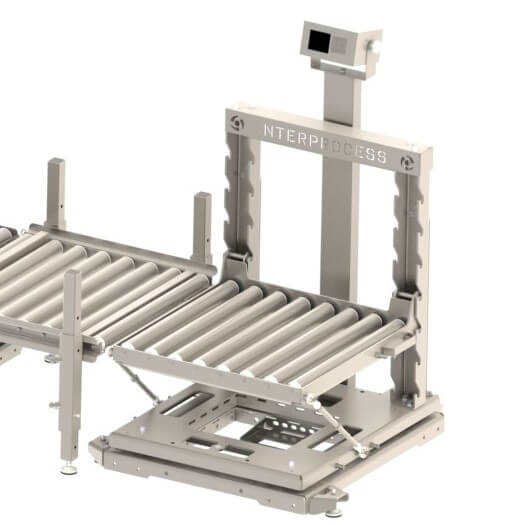
Weighing automation
We offer special weigh controllers from the Dutch company PENKO with dedicated MFL (Mono Fill) software enabling a simple and fully automated process of dust-free filling of various types of containers.
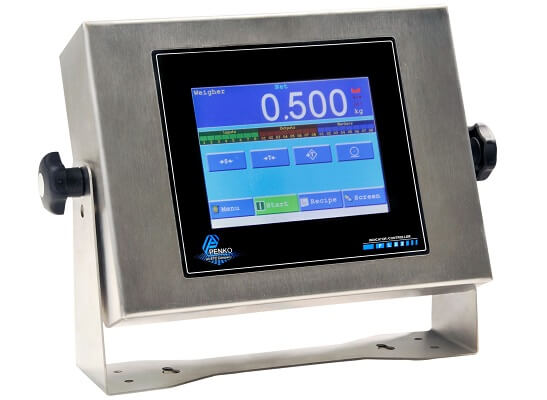
Dust-free filling process
Place the insert from the container on the filling head and close the clamp – then the container is pre-mounted. When the foot switch is pressed by the operator, the sealing process inflates, which guarantees a completely tight connection and a dust-free filling process.
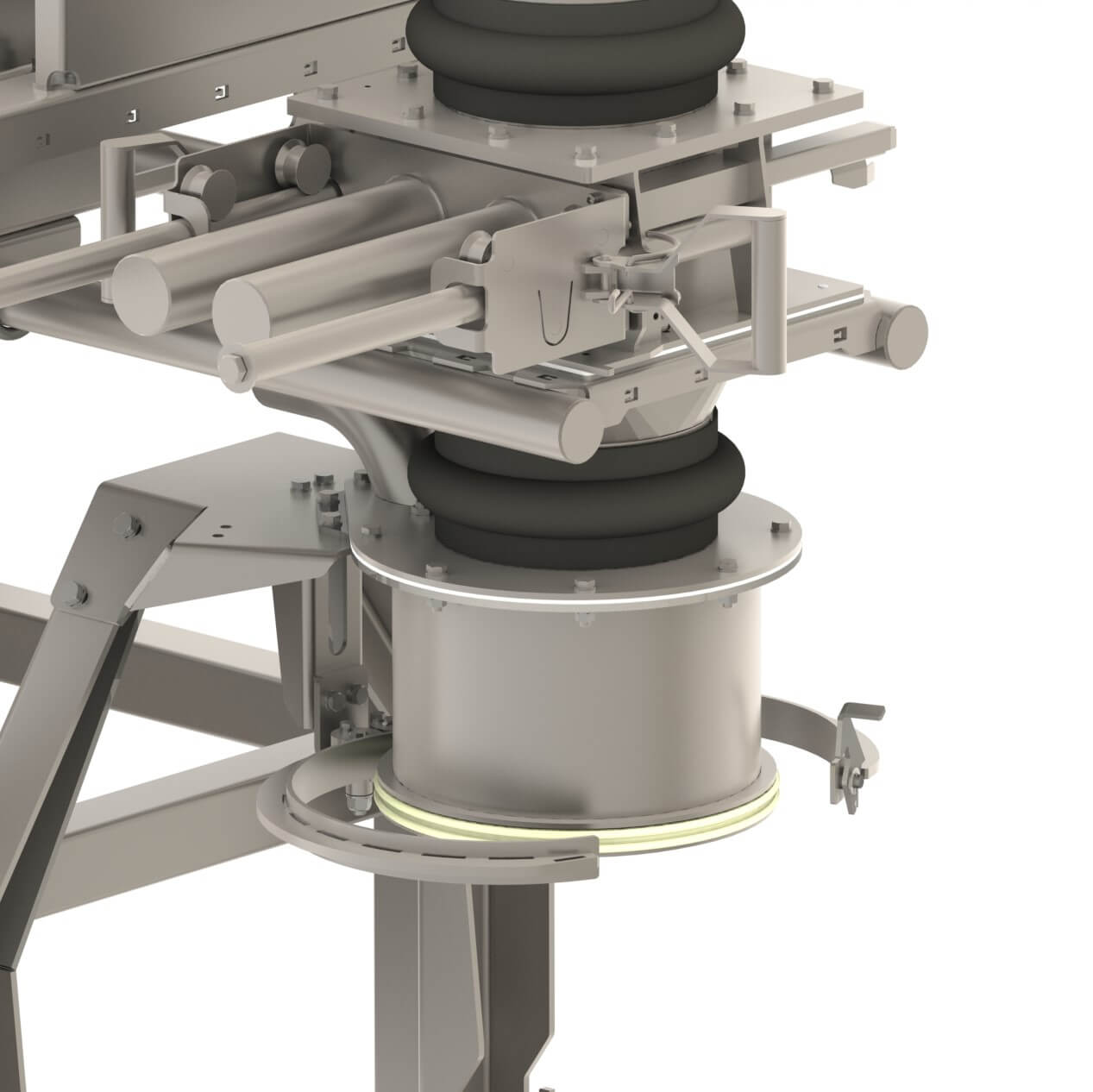
Versatility
Thanks to the use of a screw feeder with different types of feeding tools, depending on the material fed, no challenges are a problem for us. We can dosing dry bulk materials of all types – both well- and difficult-flowing, easily aerated, with a tendency to uncontrolled flow or clumping.
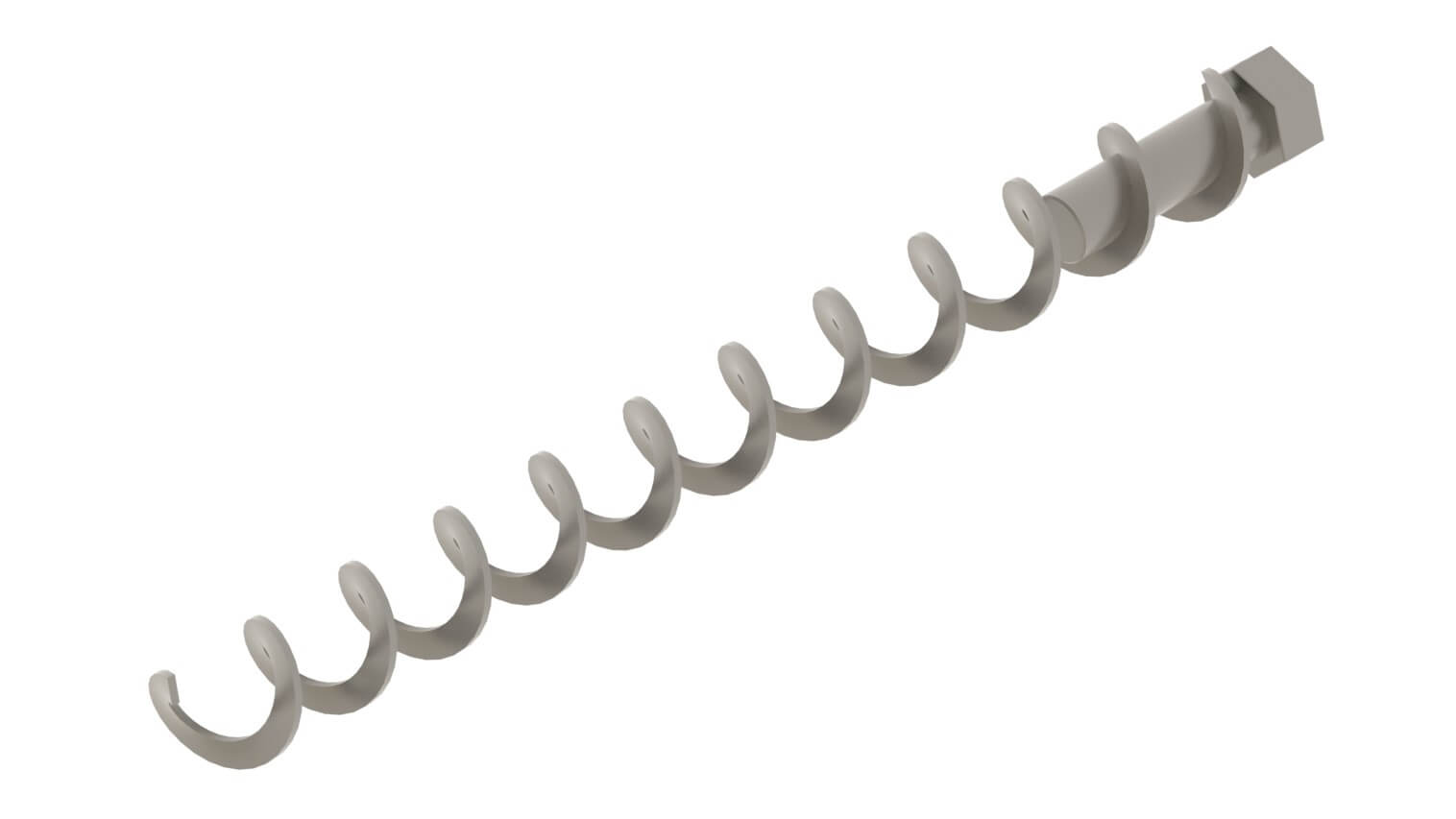
Spiral screw
Used for:
- hard-flowing material (e.g. flour, soda, granulates)
- small and viscous material and material that can collect on leading pin (e.g. cocoa, titanium white)
- material consisting of big segments that may collect and cause a great friction between leading pin and surface of through pipe
- material that requires much better hygienic conditions (e.g. food material)
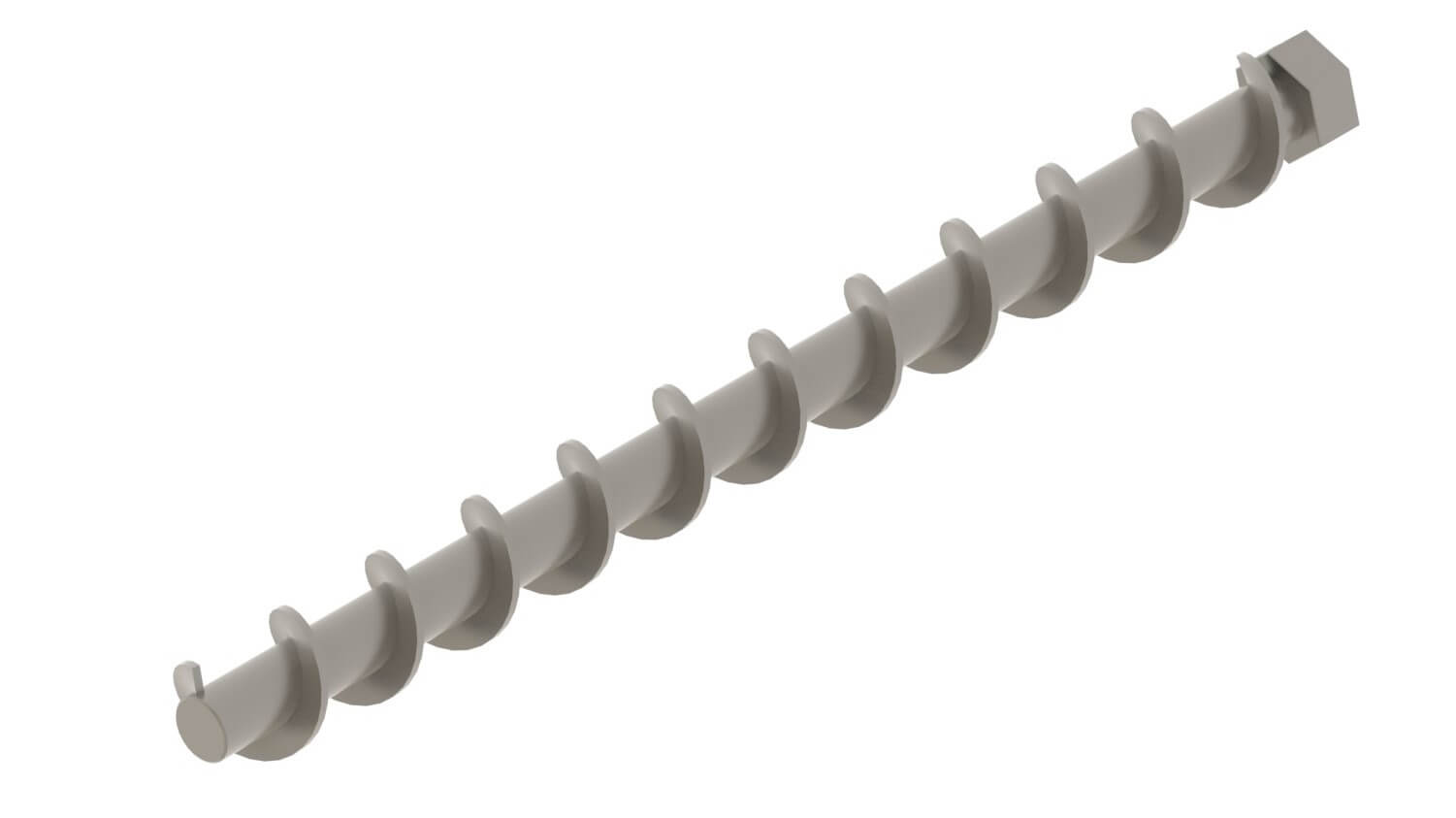
Full screw (with center rod)
Used for:
- well-flowing and very loose material (e.g. salt, sugar)
- material that easily aerates with tendency for uncontrollable flow (e.g. carbonates, gypsum)
- highly abrasive material (e.g. quartz sand)
- brittle material (e.g. flakes, soluble coffee)
Advantages
- Dust-free and accurate filling of various types of packaging
- Automated line operation thanks to PENKO SGM800, 1020, FLEX and 2100 controllers with MFL (Mono Fill) software or created individually
- The sifters guarantee that there will be no foreign particles in the packaging
- Universal solution – application for a wide range of products thanks to the use of a screw feeder
- The modular design enables custom configuration and extension of the line
- Legal-for-trade scales in the range from 10 to 100 kg
- Adaptable to potentially explosive areas (ATEX) or made of materials compliant with FDA requirements
- Individual approach to the project