- Ku Wiśle 7, 00-707 Warsaw
- +48 787 783 590
- biuro@interprocess.pl
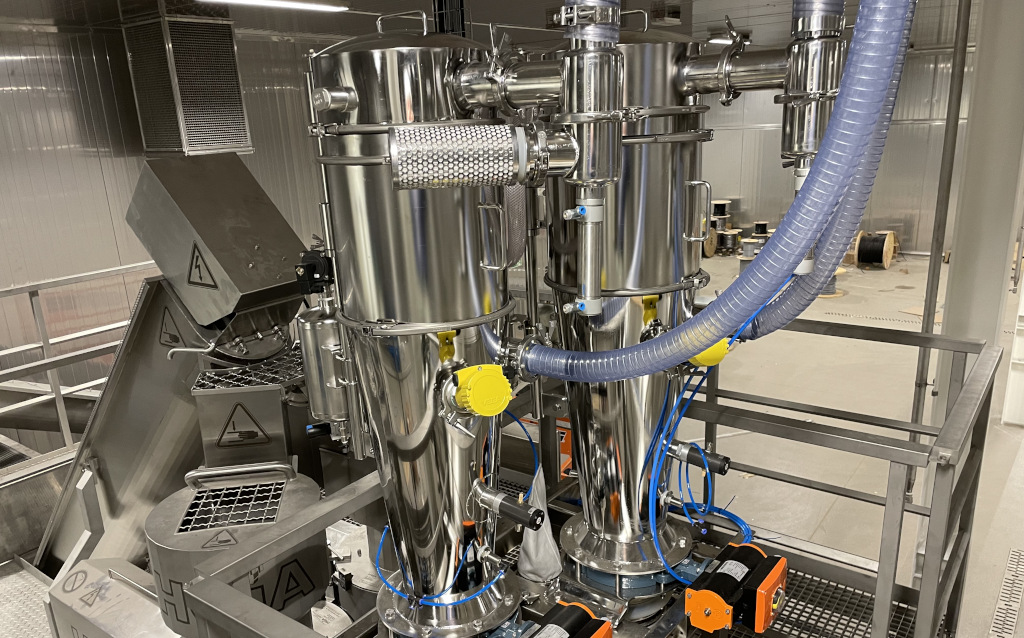
Vacuum transport is a dust-free process for handling dry bulk materials such as powders or granules using suction. Most vacuum conveying systems transfer products to a vacuum receiver based on a specific time, volume or weight. At the end of the time sequence, or when the right amount of bulk material has been obtained, the drain valve can be opened and the material being transported can be discharged from the receiver.
There are two types of vacuum transport. Transport in the dilute phase and transport in the dense phase. In the dilute phase, the material being transported is cut into the air stream and represents almost an equal part of the air and the product. This method is ideal for handling powder, such as sugar or flour.
In the case of a vacuum transfer in a dense phase, the material is transferred in the transport tubes with a higher contribution to the air and moves more slowly than during the transfer in the dilution phase. This is an excellent choice for brittle products or powder mixtures.
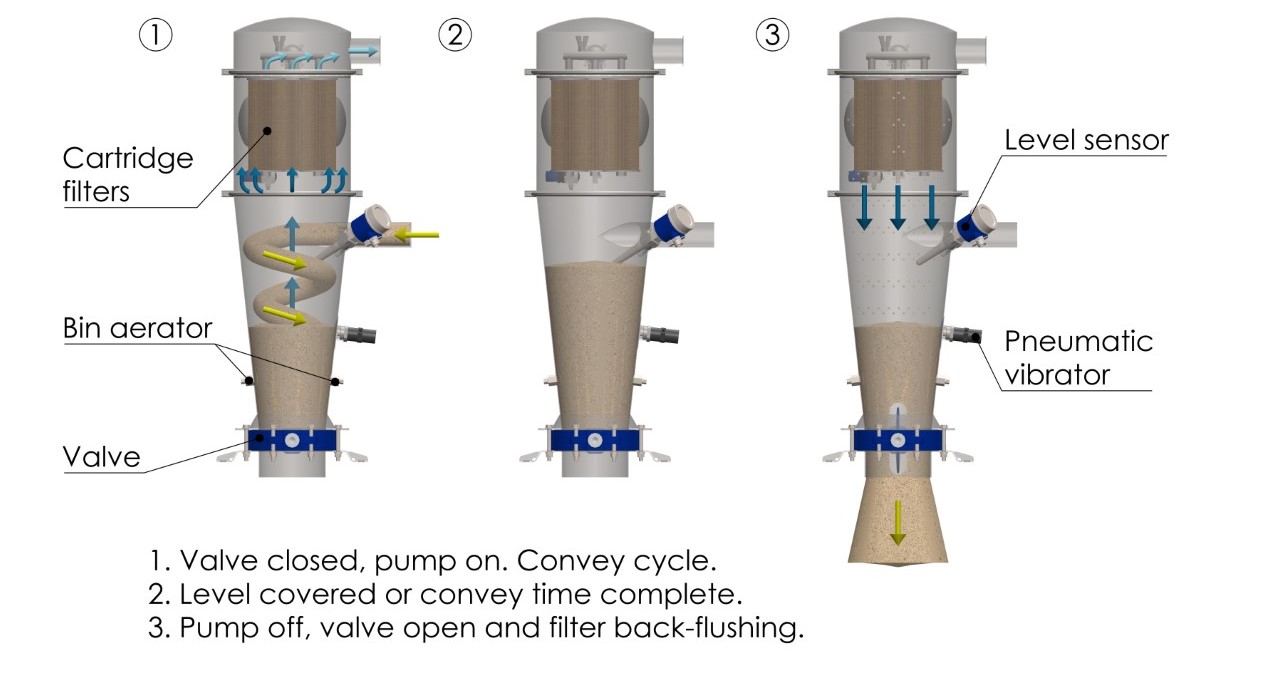
In our vacuum transport system, loading and receiving points are a key elements. These components are modular and are ready for quick disassembly. Thanks to its special sealing and comfortable locking clamps, cleanliness is extremely easy.
It takes only a few minutes to spread the complete units into the main components and access inside.
Advantages of vacuum transport
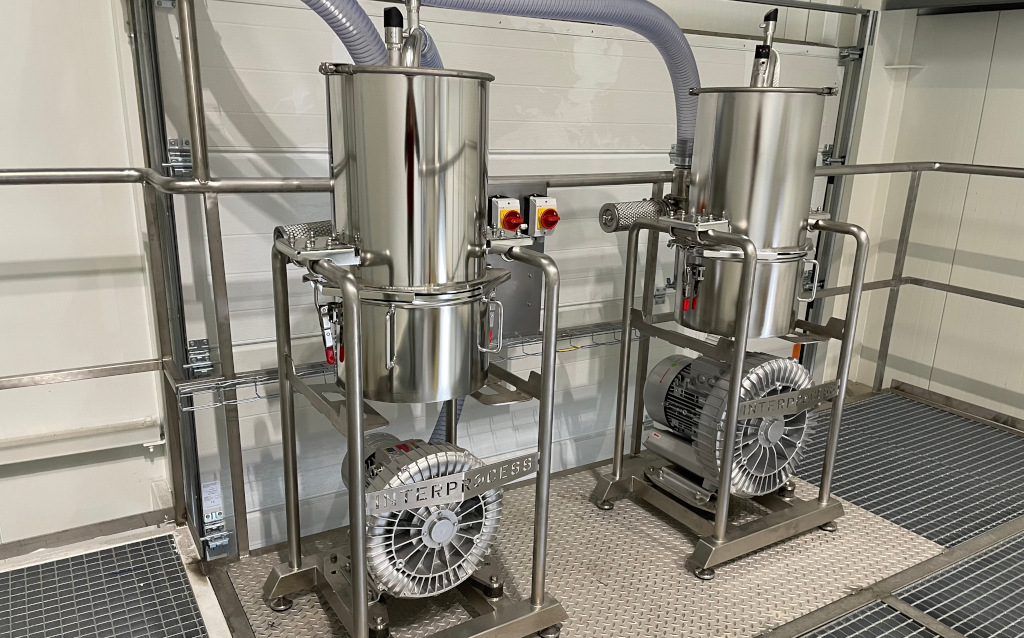
- The modular construction of the units;
- Ability to build systems with multiple loading and receiving points;
- Easy to keep clean;
- Possibility of hygienic version, with surface roughness Ra<0.8um;
- Minimal maintenance required;
- Safe in Ex areas (explosion hazards);
- Dust-free work environment;
- Small size, efficient use of space.
The basic components of the vacuum transport system.
We offer a variety of components that can work perfectly with your existing or new production process. The main element is the suction lances, which are ideal for manual emptying of bags. Another variant is the suction units from the bottom which can be installed under the tanks, the big-bag unloading stations, the bagators, or at the material dispensing site.
Transport line
In its simplest form, it connects the loading point to the receiver. On more advanced systems, it includes multi-valve (diverters), load line relief valves, magnetic separators, spreaders. The piping itself can be made of steel or plastic.
Air pneumatic receivers
Depending on the system’s performance, the size of the receiver also determines the quantity of suction in one cycle. Inside the parent unit there is a filter system with automatic thinning. The material release valve is usually located under the receiver. Alternatively, a special valve can be used to ensure continuous material flow. The receiver can also be used as a metering device, in which case it is placed on the scale on which the vacuum transport cycle is controlled.
Coupling and separating valves
The transport cycle is controlled by valves which alternately open and close allow the material to be transported alternately to the receiver or to discharge the process when the pressure at the receiver has to be balanced with atmospheric pressure. For very demanding materials, the purge valves for the pipeline are also used if there is a risk of material breakage and blockage in the transport line.